3D Printing Revolution: US Manufacturing Reshaped
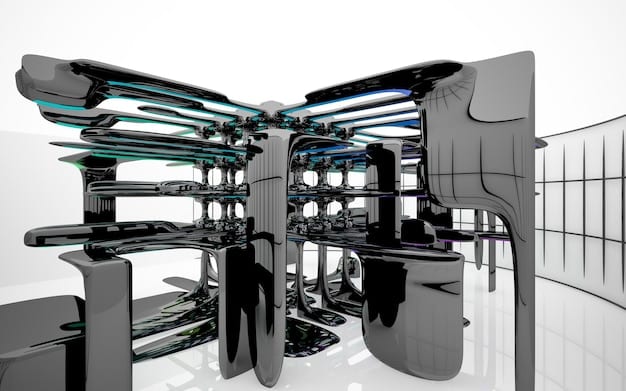
The 3D printing revolution is reshaping US manufacturing by transitioning from rapid prototyping to mass production, allowing for customized and efficient product creation.
The 3D printing industry is rapidly transforming the landscape of manufacturing in the United States. What once was a technology primarily used for prototyping is now advancing into the realm of mass production, offering new levels of customization, efficiency, and innovation. The 3D printing revolution: from prototyping to mass production in the US, promises to reshape how products are designed, manufactured, and distributed, opening up opportunities, and posing challenges for businesses across various sectors.
3d printing: a brief history
3D printing, also known as additive manufacturing, has evolved significantly since its inception. Understanding its origins and progress is essential to appreciate its current impact on manufacturing.
The early days of 3D printing
The concept of 3D printing dates back to the 1980s when Charles Hull invented stereolithography, a process that uses UV light to cure liquid polymers into solid objects. This breakthrough paved the way for the development of various 3D printing technologies.
Initially, 3D printing was primarily used for rapid prototyping, allowing designers and engineers to quickly create physical models of their designs. This significantly reduced the time and cost associated with traditional prototyping methods.
Evolution into mass production
Over the years, 3D printing technology has advanced significantly, with improvements in speed, material compatibility, and precision. These advancements have enabled 3D printing to move beyond prototyping and into the realm of mass production.
- Advancements in materials: The range of materials that can be used in 3D printing has expanded to include plastics, metals, ceramics, and composites, making it suitable for a wide range of applications.
- Increased speed and efficiency: Modern 3D printers are much faster and more efficient than their predecessors, making them viable for producing large quantities of parts.
- Improved precision: High-resolution 3D printers can produce parts with intricate designs and tight tolerances, meeting the demands of various industries.
Today, 3D printing is used in various industries, including aerospace, automotive, healthcare, and consumer goods, to produce end-use parts, tools, and customized products.
The evolution of 3D printing from a prototyping tool to a mass production method has opened up new possibilities for manufacturers. Its ability to create complex geometries, customize products, and reduce waste makes it an attractive alternative to traditional manufacturing processes.
benefits of 3d printing in mass production
The integration of 3D printing into mass production offers numerous advantages, transforming traditional manufacturing processes.
Customization and personalization
One of the most significant benefits of 3D printing is its ability to produce customized and personalized products. Unlike traditional manufacturing methods, which require large production runs to be cost-effective, 3D printing allows for the creation of individual items tailored to specific customer needs.
This capability has significant implications for industries such as healthcare, where customized prosthetics, implants, and medical devices can be produced to fit individual patients.
Faster production cycles
3D printing can significantly reduce production cycles by eliminating the need for tooling and molds. Traditional manufacturing processes often require weeks or months to create the necessary tools, whereas 3D printing can start production within hours.
This faster turnaround time enables manufacturers to respond quickly to changing market demands and reduce lead times for customers.
Cost efficiency
While the initial investment in 3D printing equipment can be substantial, it can lead to significant cost savings in the long run. 3D printing reduces material waste by only using the material needed to create the part, unlike traditional methods that involve cutting away excess material.
- Reduced labor costs: 3D printing is highly automated, reducing the need for manual labor and associated costs.
- Lower inventory costs: With 3D printing, manufacturers can produce parts on demand, reducing the need to hold large inventories.
- Elimination of tooling costs: The absence of tooling and mold costs further contributes to the overall cost efficiency of 3D printing.
The cost-efficiency of 3D printing makes it an attractive option for small and medium-sized enterprises (SMEs) looking to compete with larger manufacturers.
The benefits of 3D printing in mass production extend beyond cost savings and faster production cycles. Its ability to enable customization, reduce waste, and foster innovation positions it as a key technology for the future of manufacturing.
challenges of adopting 3d printing for mass production
Despite its numerous benefits, adopting 3D printing for mass production presents several challenges that manufacturers must address.
Scalability
One of the primary challenges is scalability. While 3D printing is excellent for producing small quantities of parts, scaling up production to meet the demands of mass markets can be difficult.
Ensuring consistent quality and throughput across a large number of 3D printers requires careful management and optimization.
Material limitations
Although the range of materials compatible with 3D printing has expanded, it is still limited compared to traditional manufacturing processes. Some materials may not be suitable for certain applications due to their mechanical properties or durability.
Research and development efforts are continuously underway to expand the material options available for 3D printing.
Skills gap
Operating and maintaining 3D printing equipment requires specialized skills and knowledge. Many manufacturers face a skills gap in their workforce, making it difficult to fully leverage the capabilities of 3D printing.
Investing in training and education programs is essential to equip employees with the necessary skills to succeed in a 3D printing environment.
Cost
While 3D printing can be cost-effective in certain scenarios, the initial investment in equipment and materials can be significant. High-end 3D printers capable of producing parts with the required precision and quality can be expensive.
Manufacturers must carefully analyze their production needs and determine whether the benefits of 3D printing outweigh the costs.
Addressing these challenges requires a strategic approach that includes investing in infrastructure, developing a skilled workforce, and collaborating with industry partners to overcome technical barriers.
applications of 3d printing in various industries
3D printing is transforming various industries, offering innovative solutions and driving new opportunities.
Aerospace
The aerospace industry has been an early adopter of 3D printing, using it to produce lightweight components, complex geometries, and customized parts for aircraft and spacecraft.
3D printing enables the creation of parts with optimized designs, reducing weight and improving fuel efficiency.
Healthcare
In healthcare, 3D printing is used to create customized prosthetics, implants, and surgical guides. These personalized solutions improve patient outcomes and reduce the risk of complications.
Additionally, 3D printing is used to create anatomical models for surgical planning and training, enhancing the precision and effectiveness of medical procedures.
Automotive
The automotive industry uses 3D printing for rapid prototyping, tooling, and producing customized parts for vehicles. 3D printing enables automakers to quickly iterate on designs, reduce lead times, and create parts with complex geometries.
Moreover, 3D printing is used to produce customized interiors and exterior components, enhancing the personalization of vehicles.
Consumer goods
3D printing is used in the consumer goods industry to create customized products, such as eyewear, footwear, and jewelry. This allows consumers to personalize their purchases and create unique items tailored to their preferences.
- Customized eyewear: 3D printing enables the creation of eyeglasses frames that are tailored to the individual’s facial features.
- Personalized footwear: Custom-fit shoes and insoles can be produced using 3D printing, improving comfort and performance.
- Unique jewelry: 3D printing allows for the creation of intricate and personalized jewelry designs.
The applications of 3D printing across various industries demonstrate its versatility and potential to drive innovation and create new opportunities for businesses.
As technology continues to advance and costs decrease, 3D printing is expected to play an even greater role in shaping the future of manufacturing.
the role of government and policy in fostering 3d printing
Government support and policy play a crucial role in fostering the growth and adoption of 3D printing in the US.
Investment in research and development
Government agencies, such as the National Science Foundation (NSF) and the Department of Energy (DOE), invest in research and development programs to advance 3D printing technology. These investments support the development of new materials, processes, and equipment, driving innovation and competitiveness.
Moreover, government funding supports collaborative research projects that bring together industry, academia, and government to address key challenges and accelerate the adoption of 3D printing.
Incentives for adoption
The government offers incentives, such as tax credits and grants, to encourage manufacturers to adopt 3D printing technology. These incentives reduce the financial burden of investing in new equipment and training, making it more accessible for SMEs.
Additionally, the government provides technical assistance and support to help manufacturers integrate 3D printing into their operations.
Standards and regulations
Developing standards and regulations for 3D printing is essential to ensure the quality, safety, and reliability of 3D-printed products. Government agencies, such as the National Institute of Standards and Technology (NIST), work with industry stakeholders to develop standards and guidelines for 3D printing processes and materials.
- Material testing: Establishing standards for material testing ensures that 3D-printed parts meet the required mechanical properties and durability.
- Process control: Developing guidelines for process control helps manufacturers maintain consistent quality and repeatability in their 3D printing operations.
- Safety regulations: Implementing safety regulations ensures that 3D printing processes do not pose health or environmental risks.
These standards and regulations build confidence in 3D printing technology and facilitate its adoption across various industries.
Government policies that promote innovation, provide incentives for adoption, and establish standards and regulations are essential for fostering the growth of 3D printing and ensuring its long-term success in the US.
future trends in 3d printing and mass production
The future of 3D printing holds immense potential as technology continues to evolve and new innovations emerge.
Advancements in materials
One of the key trends in 3D printing is the development of new materials with improved properties and performance. Researchers are working on creating materials that are stronger, lighter, and more durable, expanding the range of applications for 3D printing.
Additionally, there is a growing interest in sustainable materials, such as bio-based plastics and recycled metals, reducing the environmental impact of 3D printing.
Integration with AI and machine learning
The integration of artificial intelligence (AI) and machine learning (ML) is transforming 3D printing processes. AI and ML algorithms can optimize designs, predict potential failures, and improve process control, enhancing the efficiency and reliability of 3D printing.
Moreover, AI and ML can enable the creation of self-correcting 3D printers that automatically adjust parameters to ensure consistent quality.
Distributed manufacturing
Distributed manufacturing, where 3D printers are located in multiple locations and connected through a digital network, is becoming increasingly popular. This approach enables manufacturers to produce parts closer to their customers, reducing lead times and transportation costs.
- On-demand production: Distributed manufacturing allows for on-demand production, where parts are produced only when needed, minimizing inventory costs.
- Localized customization: 3D printers can be located in retail stores or service centers, enabling localized customization and personalized products.
- Resilient supply chains: Distributed manufacturing enhances supply chain resilience by diversifying production locations and reducing reliance on centralized factories.
These future trends promise to unlock new possibilities for 3D printing, driving innovation and transforming manufacturing processes.
As technology continues to advance, 3D printing is poised to play an even greater role in shaping the future of manufacturing in the US and around the world.
Key Point | Brief Description |
---|---|
🚀 Prototyping to Production | 3D printing is transitioning from rapid prototyping to full-scale mass production. |
⚙️ Benefits | Customization, faster cycles, and cost efficiency drive 3D printing adoption. |
🚧 Challenges | Scalability, material limits, and skill gaps are obstacles to overcome. |
🏢 Applications | Aerospace, healthcare, automotive, and consumer goods benefit from 3D printing. |
FAQ
▼
The primary advantage is the ability to create customized products on a large scale, which is not feasible with traditional manufacturing methods.
▼
3D printing uses only the material needed to create the part, minimizing waste compared to traditional subtractive methods like machining.
▼
Key industries include aerospace, healthcare, automotive, and consumer goods, each leveraging the unique benefits of additive manufacturing.
▼
The government invests in research, offers incentives for adoption, and develops standards to ensure the safety and reliability of 3D printing.
▼
Future trends include advancements in materials, integration with AI and machine learning, and the rise of distributed manufacturing networks.
Conclusion
In conclusion, the 3D printing revolution is transforming manufacturing in the US by enabling customized mass production, reducing waste, and fostering innovation. While challenges remain, ongoing advancements and supportive policies are paving the way for widespread adoption across various industries, promising a future where products are designed and manufactured with unprecedented efficiency and personalization.